「工場の5s」4つの活動事例を紹介!
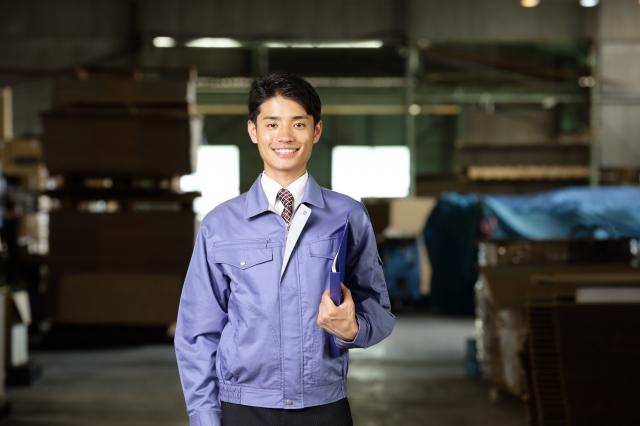
人間が生活に必要な日用品の多くは工場で製造され、大規模な工場になればなるほど品質管理が極めて難しくなります。このような事情もあって、多くの工場では独自の方式によって各部門における環境管理を進めていることも少なくありません。
日本国内の工場であればまだ良いですが、日本語の分からないスタッフも非常に多い海外の製造拠点になると、国民性の違いもあって衛生や管理意識の違いが明確になっているでしょう。
これを1つのメーカーとして各工場を統一的に管理するために5sと呼ばれるコンセプトが導入されることが多くなっているのです。
5sは工場の健全な長期的運営に必要不可欠だとされていますが、今回はこの5s活動の意義や活動事例に関してご紹介していきます。
工場の5sとは何を指してどう活用するの?
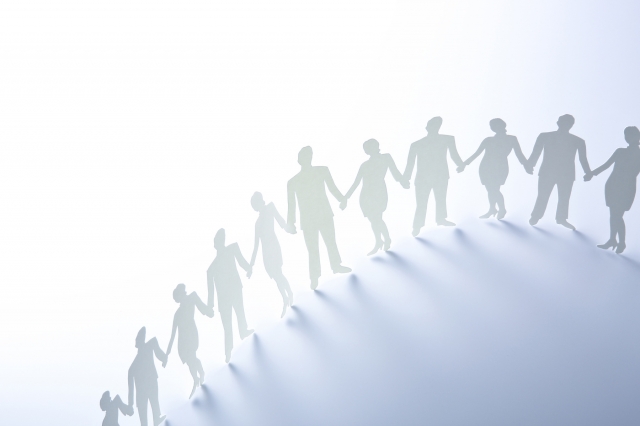
工場の管理の基本となっている5sですが、これは一体何を指しているのでしょうか?
5sはその名のとおり、5つのs(整理/整頓/清掃/清潔/しつけ)を意味しており、工場に所属するスタッフが入れ替わってもスムーズに管理維持ができるように構築された運営方針です。
工場が取得することを目指すISOなどの基準は5sが徹底されていないと取得が困難になることも多く、取得前にこれにしたがって工場内を整えていくことが一般的と言えるでしょう。
日本の製造現場から始まった環境維持コンセプト
5sの環境維持コンセプトは日本から始まり、それが世界中の工場で導入されている状況です。これは日本の製品の品質が世界で評価されていることの表れでもあり、多くのメーカーがそれを目標にしていると言っても過言ではありません。
日本における品質管理の概念は、海外のそれとは非常に大きく異なっています。日本人はモノを作る場合に上手く作ることを意識して製品不良を出さないことにこだわりますが、多くの国ではとりあえず製造して製品不良を省く管理方式を持っている訳です。
日常的な品質へのこだわりは、常日頃からの衛生管理を確実に伴っていなければ意味がないでしょう。そのため、日本発祥の5sは日本の品質レベルに近付くための重要な方法と考えられています。
拠点が海外になればなるほど5sは重要視される
この5sは経済のグローバル化が進めば進むほど重要な存在になり、製造拠点を海外に持つメーカーはこれをいかにスムーズに現地のスタッフに教育できるかがその後の発展の大きなカギになるでしょう。
近年は海外の新興国における安い労働力を当てにして、拠点を海外に移すことも少なくないですが5sの徹底が予想以上に上手くいかないこともあって理想的な品質が達成できないこともあるのです。
国家によっては5sの概念が生活習慣として重要視されていないこともあって、職場でそれを徹底することがより困難になるケースも少なくありません。
また、5sがスムーズに導入できたところは、現地スタッフとのコミュニケーションも良好であるところが多くなる傾向にあります。
オフィスにおける5s活動事例を紹介
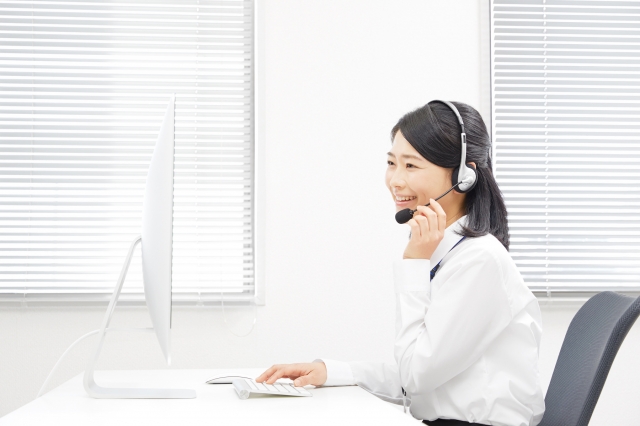
さて、工場と言ってもいろんな部門がありまして、管理部門になりますとオフィスにスタッフが集結していることも少なくありません。
管理部門の工場での役割は、製造部門がいかに不良品を出さないように管理することにあるのです。多くの管理オフィスでは管理が徹底されていないことも非常に多かったのですが、最近は5sの導入増加についても管理部門が主導で行っていることも多いでしょう。
ここでは、オフィスでの5s活動事例を紹介していきます。
ファイリングシステムによる文書管理
オフィスで最も厄介なのは文書の管理で、工場は毎日のように製造指示書や製品の仕様書を扱うこともあってまさに文書の管理は大きな業務の1つです。
文書の多さにもよりますが、クリアファイルですべての文書を管理することは基本的に不可能です。これでは、文書に対して整理/整頓を進めることはまず無理でしょう。
この場合、ファイリングシステムと呼ばれる文書管理方式を採用することが多くなっているのです。これはパソコンのフォルダの実物版になり、すべての文書を単独のフォルダに入れることになります。
フォルダは専用のキャビネットに収納され、必要に応じて取り出すことになるでしょう。これは特定の人間が文書を占有しない大きなメリットがあり、誰が休んでもどこに文書があるのかを明確にできる画期的な管理方式です。
オフィスフロアーとクリアデスクの導入
また、5sの概念をオフィスに取り入れる場合、多くのところで実行されているのがオフィスフロアーとクリアデスクになります。
オフィスフロアーは直接5sとは関係ありませんが、電気配線を一段あげた床下に組み込むことで床を歩くときにも安全になり、清掃も極めてやりやすくなるでしょう。
クリアデスクは、文字通りに机に何も置かない状態で、仕事に必要なものはキャビネットなどに入れておくことが求められるのです。
これは先述のファイリングシステムと並行して導入すると効率的な管理が可能になり、最初の準備段階では苦労しますが、導入後はスッキリとしたオフィス空間になって仕事のミスも大きく減少するメリットがあります。
製造部門における5s活動事例を紹介
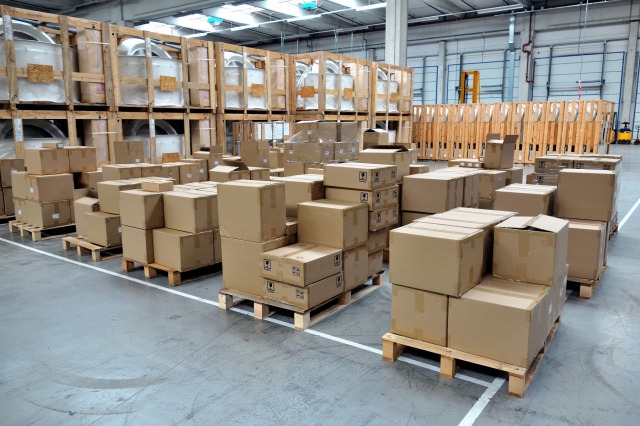
さて、工場におけるメインは製造部門になりますが、管理部門における5s活動の方法とは対して大きな差はありません。
しかし、品質の維持に関して特に重要な取り組みは存在していて、商品への異物の混入などあってはならない事態を未然に防止できます。ここでは、2つの活動をピックアップして紹介しましょう。
工具の設置場所にしっかりと枠と名称を付ける
工場では大きな製造機器以外にも、小物に近い工具も多く存在しています。工場の規模によってはこれが無数に存在することもあり、日常的に使用するスタッフもいつもどこに置いたかを忘れるくらいです。
これは、日本人でもこのような状況はありますが、海外の拠点に行けば頻繁に起こりうる事例になるでしょう。商品によっては直接段ボールに工具が混入してしまい、クライアントのところに輸出されることも少なくありません。
このような事例はクライアント側でクレームに発展するケースもあり、メーカー側では工具の設置場所を詳しく設定しておくことが求められます。
現在の工場では専用の置き場にテープで枠を作り、そこに名称を書いて仕事が終わると必ず元の位置に戻す動作を進めていることがほとんどです。
工場では意外にできていないごみの分別を徹底
また、海外拠点の製造部門でよくあるのがゴミの分別が徹底されていないことです。工場からのゴミは産業廃棄物になるため、すべて一緒にして廃棄することも多いでしょう。
海外では日本ほど分別意識が整っていないこともあり、多くの海外スタッフはすべてのゴミを同じゴミ箱に入れがちです。これは、品質を見極める上で判断基準を低下させる大きな原因となります。
日本のように可燃物や不燃物そしてプラスチックなど、廃棄する時点で属性を考える習慣をつけることは製造における品質管理にも正しい考慮を進められるようになるのです。
現在はすでに6sもしくは7sも存在している?
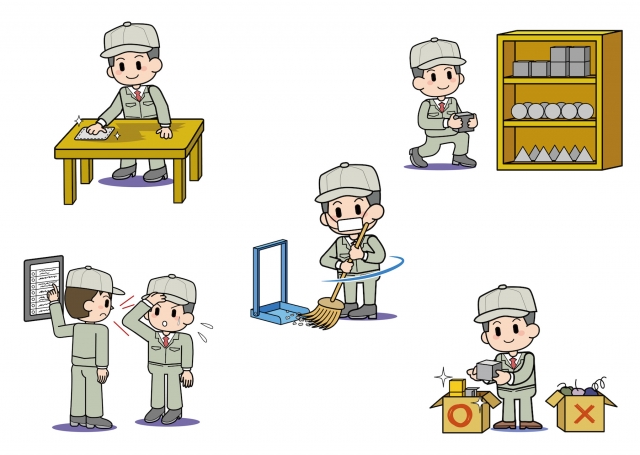
実のところ、5sは今も進化し続けていまして、すでに6sや7sへと管理項目を追加しているところもあります。
基本となる5sを守ることができるのは当たり前のことという認識の下、メーカーにとっても競争の激しい現代社会においてより発展するためには他社にはできない独自の環境管理が求められるのは間違いありません。
ここでは、6sや7sで追加される代表的項目の説明やその意義までもチェックしていきましょう。
セキュリティや作法など企業によって追加ポリシーが異なる
工場などで進められる6sと7sについては、いわゆるセキュリティや作法が追加ポリシーとして採用されることが多くなります。
このうち、セキュリティは数多くの工場に採用されていて、非常に意識されやすい6sと言えるでしょう。日本語では安全を意味しますが、海外拠点ではSecurityと言った方が分かりやすいので代替的に6sに使いされている訳です。
かつての日本のメーカーでも工場内における労働災害については重要視してこなかった時代もあるのですが、海外拠点で労働災害が起これば国家問題に発展することもあるのでメーカーが特に力を入れています。
作法に関しては導入しているところはまだまだ少ないものの、日本文化を製造に取り入れているところでは非常に有用なポリシーとなるでしょう。